Evaluating Adhesion of Hot-Rubberized Asphalt Membrane to Moisture Mitigation Coatings
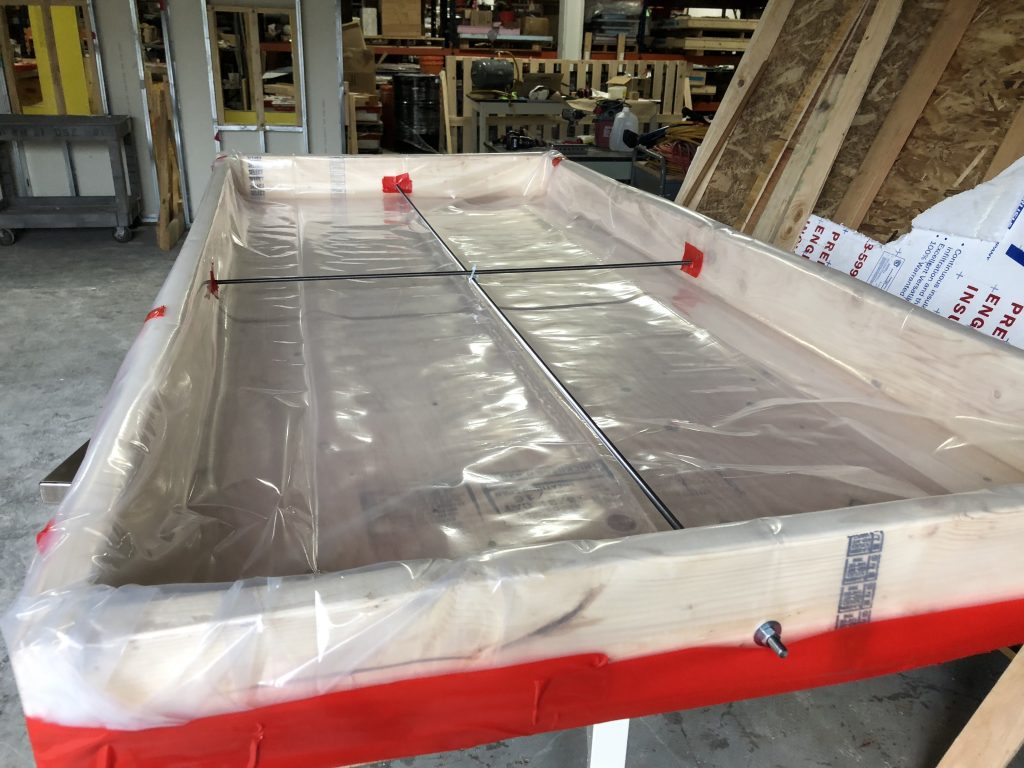
Hot-applied rubberized asphalt (HRA) is a monolithic, reinforced, asphaltic waterproofing membrane typically used on concrete roofs or plaza decks in a protected-membrane roof configuration. HRA membranes covered with overburden on sloped concrete substrates have demonstrated successful performance for several decades. The advantages of HRA include seamless composition, single-component installation, broad installer familiarity, and an ability to accommodate and confirm to irregular substrate profiles.
HRA’s robust and continuous bond to concrete substrates provides dimensional stability for the membrane and limits the potential for water to migrate away from the membrane breaches. These properties are important for the increasingly popular uses of HRA where overburden materials are significantly more invasive and more costly to remove than utility pavers or gravel ballast. For a continuous mechanical bond to form between HRA and concrete, the concrete must be free of dust and debris, have a textured surface profile, and be “sufficiently dry.” The HRA manufacturers’ requirements vary, but typically reference a minimum 14- or 28-day waiting period after concrete placement. However, on a construction site, achieving a “sufficiently dry” concrete substrate can be a formidable challenge and may ultimately take weeks or months. Installing HEA on insufficiently dry concrete may affect not only the initial HRA bond but also the long-term bond, as the concrete moisture-vapor drive has the potential to reduce adhesion or debond membranes over time. The roofing industry is well aware of these risks and continues to advance studies on the effects of moisture in concrete decks.
HRA remains a good choice for many applications, but increasingly tight construction schedules may not afford the time needed to sufficiently dry concrete decks for HRA application. To accelerate substrate readiness for HRA, some construction teams have begun applying epoxy moisture mitigation coatings (MMCs) to the concrete substrate prior to applying HRA. The intent is to retard concrete moisture vapor emission and provide a substrate that can be ready for HRA faster than bare concrete would be. These topical treatments are traditionally used in the context of interior floor coverings, but similar treatments are used as a primer for cold fluid-applied waterproofing membranes in exterior applications with a reasonable track record. This approach has been reported to prepare the coated surface of the concrete for HRA application in as few as six days after concrete placement.
Despite the added labor and cost of MMCs, the promise of an accelerated schedule is attractive to contractors and project stakeholders. As with any innovation in construction technology; however, vetting is necessary to assess the merits and drawbacks of this new approach. We developed and executed the testing program described in this paper to support the roofing industry’s vetting of this approach. Specifically, our primary objectives include exploring the following questions:
- How does the adhesion of HRA to MMC products compare with HRA adhesion to uncoated concrete?
- Does broadcasting sand into MMC improve HRA-to-MMC adhesion relative to otherwise smooth cured MMC surface?
- Is the adhesion of HRA to MMC affected by the dry time of the concrete under the MMC (such as, at 7 days versus 14 days)?
- Does the adhesion of HRA to MMC change over time (such as, from initial installation to 18 months after installation)?
Publisher
IIBEC Interface