Corrosion Mitigation Strategies for Parking Structures
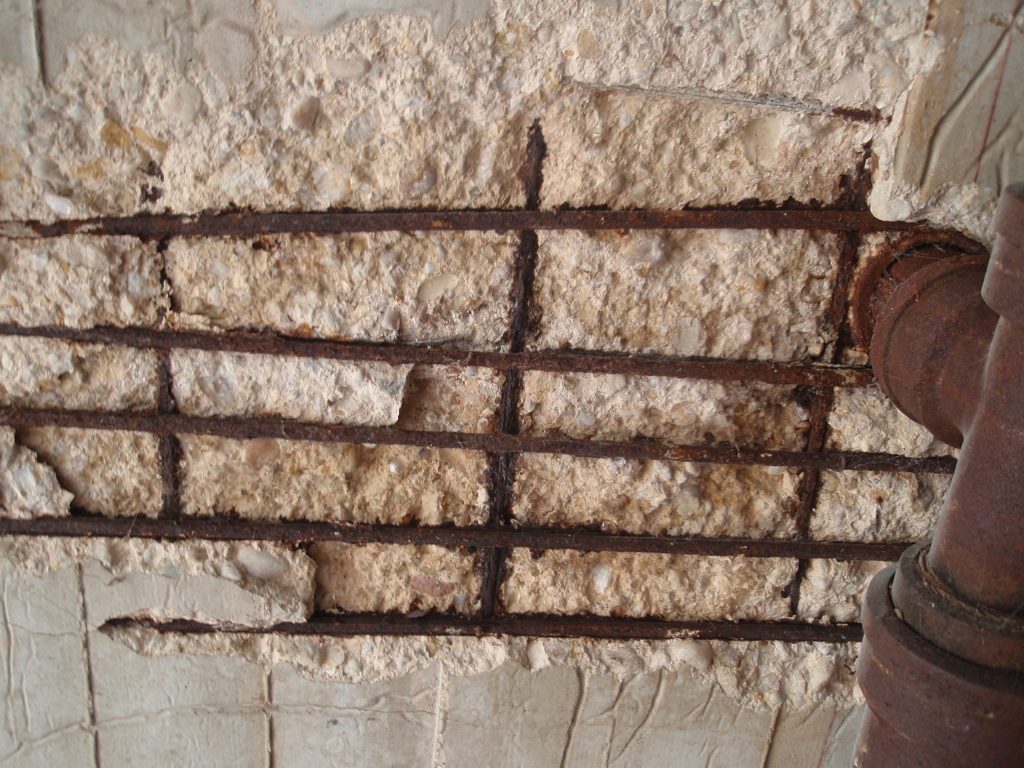
Parking structures in cold climates are exposed to more severe conditions than most other buildings. Vehicles bring in rainwater, snow, and deicing salts. Roof-level areas are directly exposed and perimeter areas of open parking structures are indirectly exposed to windblown rain and snow. Open, unheated parking garages must endure large daily and seasonal temperature variations.
Parking structures constructed up until the mid-1980s were designed with what has turned out to be inadequate corrosion protection, and owners and managers are now faced with decisions about how best to extend the useful life of these deteriorating assets. Fortunately, structural engineers can employ several corrosion mitigation technologies individually or in combination to slow, and in some instances potentially stop, ongoing corrosion damage.
The Causes of Corrosion
The practice of applying salts to keep roads free of ice began in earnest in the early 1960s and increased tenfold by the early 1970s. By the late 1960s, bridges in cold climates began to experience delamination and spalling of concrete over corroding reinforcement. By the early 1970s, bridge engineers learned that deicing salts were destroying the natural corrosion protection provided by concrete. Shortly thereafter, parking structure engineers came to the same realization when they found that parking garages were also suffering from reinforcement corrosion.
Once corrosion begins, it continues where concrete is chloride-contaminated (from deicing salts) or carbonated (a slowly occurring chemical reaction between the concrete and carbon dioxide in the air that reduces the alkalinity of the concrete). Structural engineers who investigate distressed concrete parking structures must understand the cause of the corrosion and the degree of chloride contamination or carbonation through in situ and laboratory testing of concrete samples.
Based on these findings, consultants can then develop appropriate corrosion mitigation strategies that adhere to project budgets and desired outcomes. These can be categorized as external or internal protection systems.
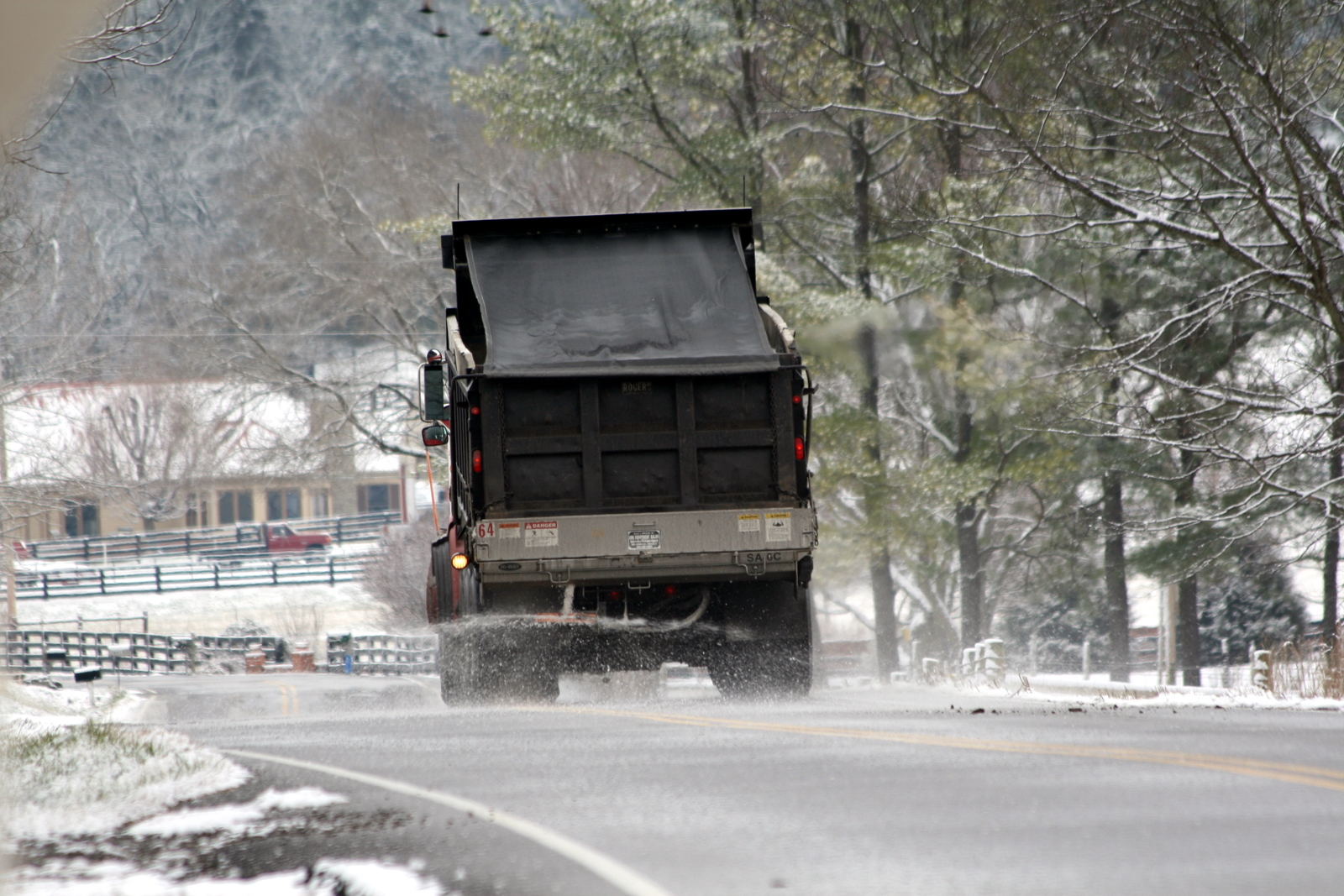
External Corrosion Mitigation Systems
Generally, external systems are surface-applied fluids that slow, but do not halt, corrosion by reducing moisture and airflow into the concrete.
- Sealers: Clear, penetrating, water-repellent sealers reduce moisture flow into exposed concrete. Penetrating sealers are not a complete barrier (i.e., they do not span cracks) and they must be reapplied periodically, usually about every five to seven years.
- Waterproofing coatings: Liquid-applied waterproofing coatings are opaque and typically heavy-bodied. They reduce moisture flow into concrete at critical surfaces such as roofs or decks. These coatings typically need a wearing surface recoat every five to ten years, depending on exposure to wear.
- Elastomeric and anticarbonation coatings: Opaque elastomeric or anticarbonation coatings protect exposed concrete from a range of elements (moisture, chloride, carbonation, acid rain, etc.). Anticarbonation coatings must be reapplied periodically, usually about every ten to fifteen years.
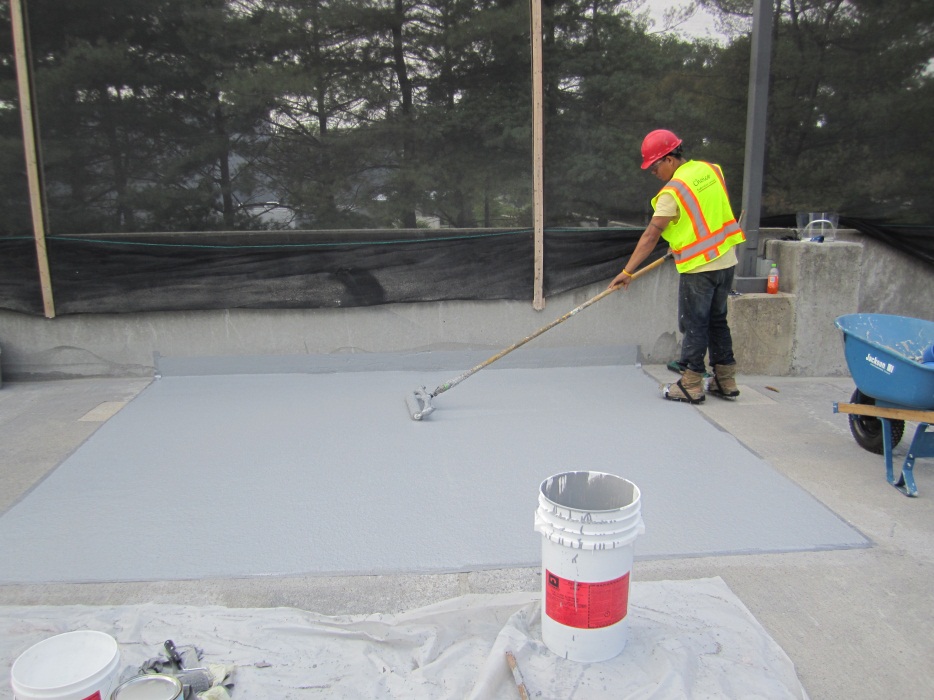
Internal Corrosion Mitigation Systems
Generally, these treatments work at the subsurface level by chemically altering the concrete or reinforcing steel, or by electrically changing the internal microclimate within the concrete. In this way, some of these measures can address or reverse internal root causes of reinforcement corrosion.
- Corrosion inhibitors: Migratory corrosion inhibitors are chemicals applied to the concrete surfaces that migrate through the concrete to embedded steel where they interfere with the corrosion process and slow the rate of corrosion. Corrosion inhibitors might require reapplication depending on the severity of exposure. Migrating corrosion inhibitors are clear, penetrating fluid applications. The depth of penetration of the corrosion inhibitor and the location of the embedded steel must be considered for these systems to be effective.
- Cathodic protection: Cathodic protection, which controls the corrosion of the reinforcing steel with impressed electric current, can stop corrosion of the embedded steel. The applied current is very low and power consumption is negligible. The system requires slots and holes cut into the concrete surface that are repaired, but this process can alter the appearance of the original concrete surface. Surface-mounted conduits and junction boxes will also be noticeable alterations to the concrete surface. Intermittent monitoring and yearly maintenance of these systems is critical to the long-term performance of these systems.
- Chloride extraction: Chloride extraction uses a temporary application of an electric field to the reinforcement. This technology requires a conductive mesh of titanium or steel attached to the concrete surface. The process must be applied and run for several weeks to achieve results. When the process is complete, the chloride in the concrete is greatly reduced, after which, the titanium mesh is removed. This process addresses the primary root cause of the corrosion of steel reinforcement and the consequent spalling and deterioration of the concrete. Chloride extraction will not alter the appearance of the exposed cast-in-place concrete.
- Realkalization: Realkalization permanently restores the protective alkalinity of the concrete through the temporary application of a highly alkaline fluid or paste, in combination with an electric field to the reinforcement. This involves the application of a titanium mesh (as a temporary anode) and a fabric to the surface of the concrete. The process must be applied and run for several days to achieve results, after which, the titanium mesh and fabric are removed. Realkalization will not alter the appearance of the exposed cast-in-place concrete.
- Galvanic anodes: Galvanic anodes are passive corrosion inhibitors that are connected to embedded steel reinforcement to create an active voltage. The difference in potential between the anode and the steel reinforcement causes the galvanic anode to corrode in lieu of the steel. They are easily installed within the concrete repair material, are less expensive than cathodic protection, and do not require a power source or monitoring. Galvanic anodes are a low-cost solution to increase the durability of the repair concrete and adjacent parent concrete.
Conclusion
Some of the corrosion mitigation technologies described above do not have a long use history. Consequently, engineers may recommend trial installations of one or more of these techniques to monitor their effectiveness. Trial installations provide useful information for selecting corrosion mitigation measures for future repair and protection efforts on the structure. With many repair and mitigation options now available, owners and facility managers can use consultants to assist them in selecting an appropriate option by evaluating and comparing costs and service life expectations.