The Science of Fireproofing in Construction
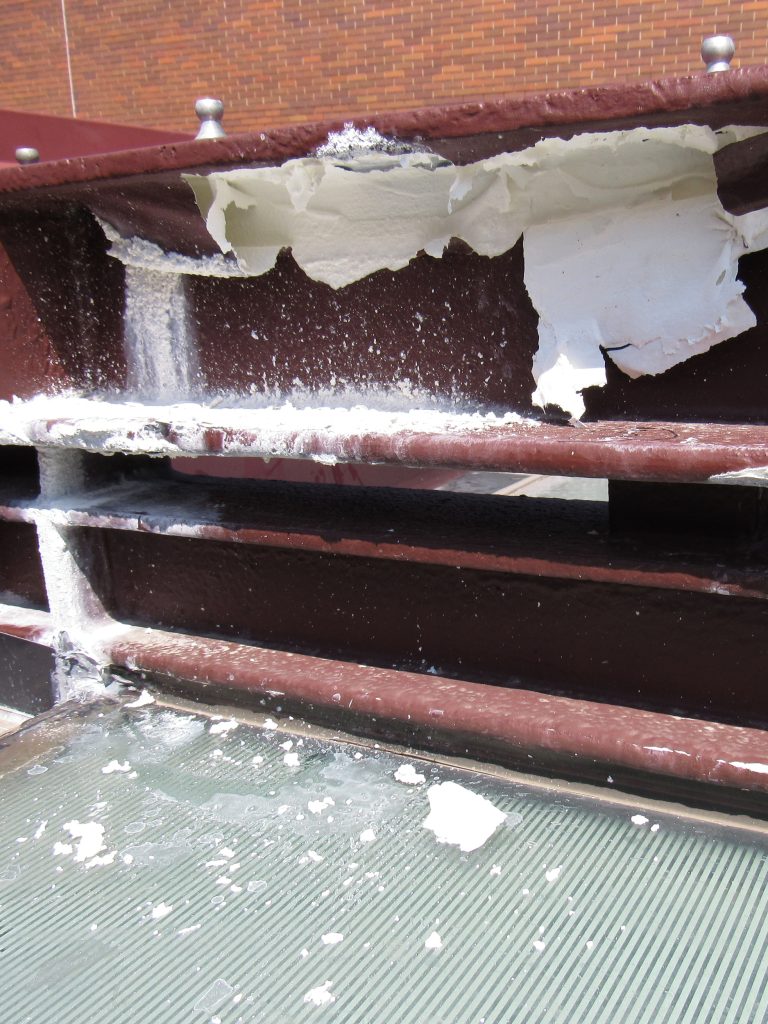
Fireproofing materials are often used in building materials to meet fire safety codes. They’re a key design element that protects critical structural and building systems during a fire to help occupants evacuate safely. While these materials are ubiquitous in building materials, it is helpful for designers and project team members to understand how they work and where they should be applied to maximize their effectiveness. Often, it can be helpful to analyze these materials in a laboratory setting to understand their chemical makeup and determine why they may succeed or fail in the field.
HOW DOES FIREPROOFING WORK?
Fire retardants are often applied as a coating to building materials as part of the fireproofing design process. Occasionally, fire retardants can be additives mixed into the building materials themselves to improve fire ratings.
A fire needs three things to start and continue burning: an ignition source, fuel (something to burn), and oxygen. Fireproofing works by disrupting one or more elements of this fire triangle by insulating the fuel to slow heat transfer, producing gases that dilute oxygen, or undergoing chemical reactions that prevent ignition or slow the spread of flames.
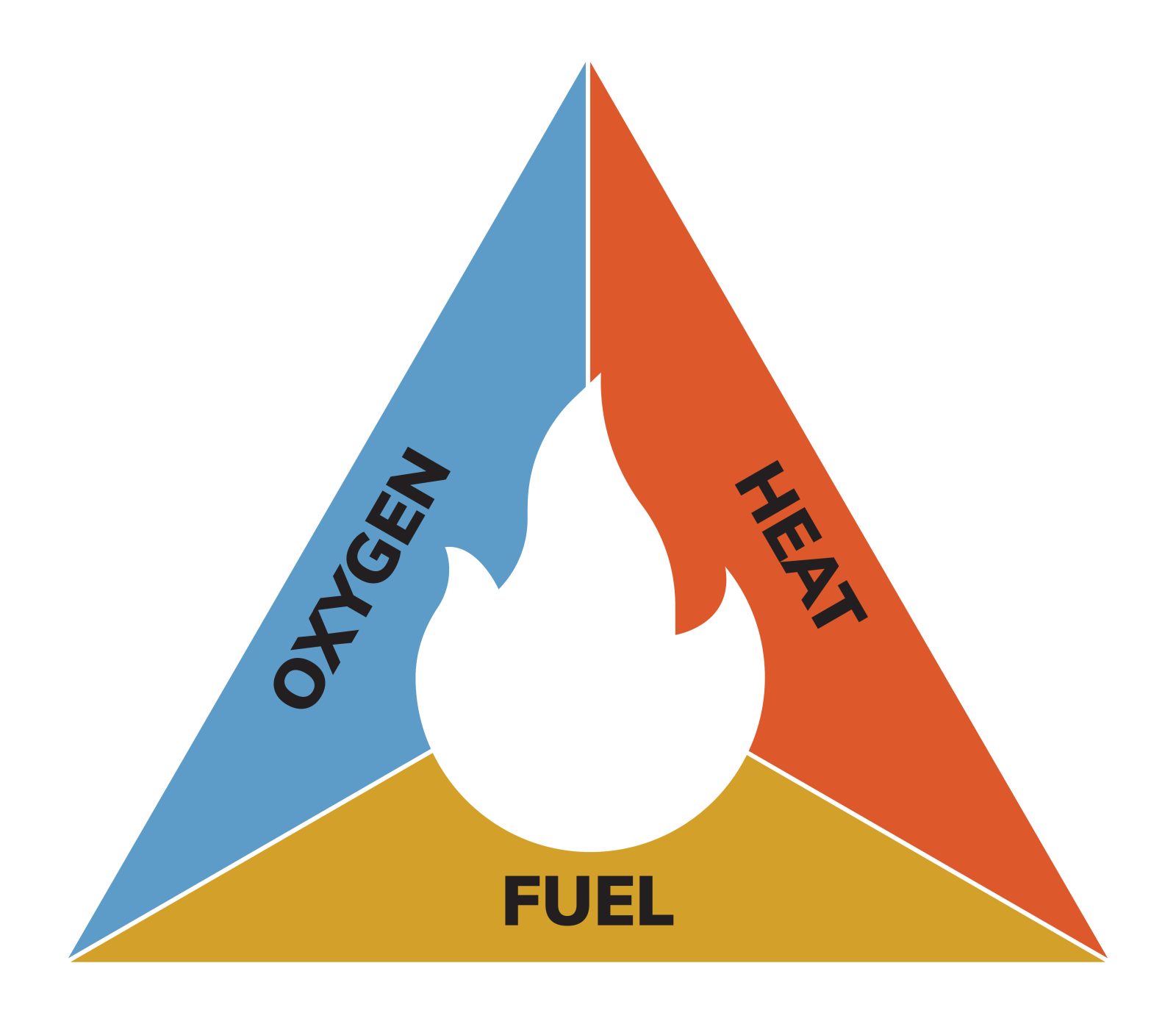
Fire-resistive material coatings
Spray-applied fire-resistive material (SFRM) might be the first thing that comes to mind when thinking about fire retardants in construction. These are available as a wet or dry formula that can be sprayed or troweled onto a surface that needs to be protected. They are often applied to primary structural steel and horizontal assemblies to protect them from heat in the event of a fire. SFRMs are typically a gypsum or Portland cement mix that hardens into a foam-like texture.
Alternatively, intumescent fire-resistant materials (IFRM) are coatings that swell when exposed to heat, creating an insulating layer.
Both SFRMs and IFRMs act as thermal barriers, insulating and protecting the underlying material by slowing heat transfer and buying valuable time during a fire.
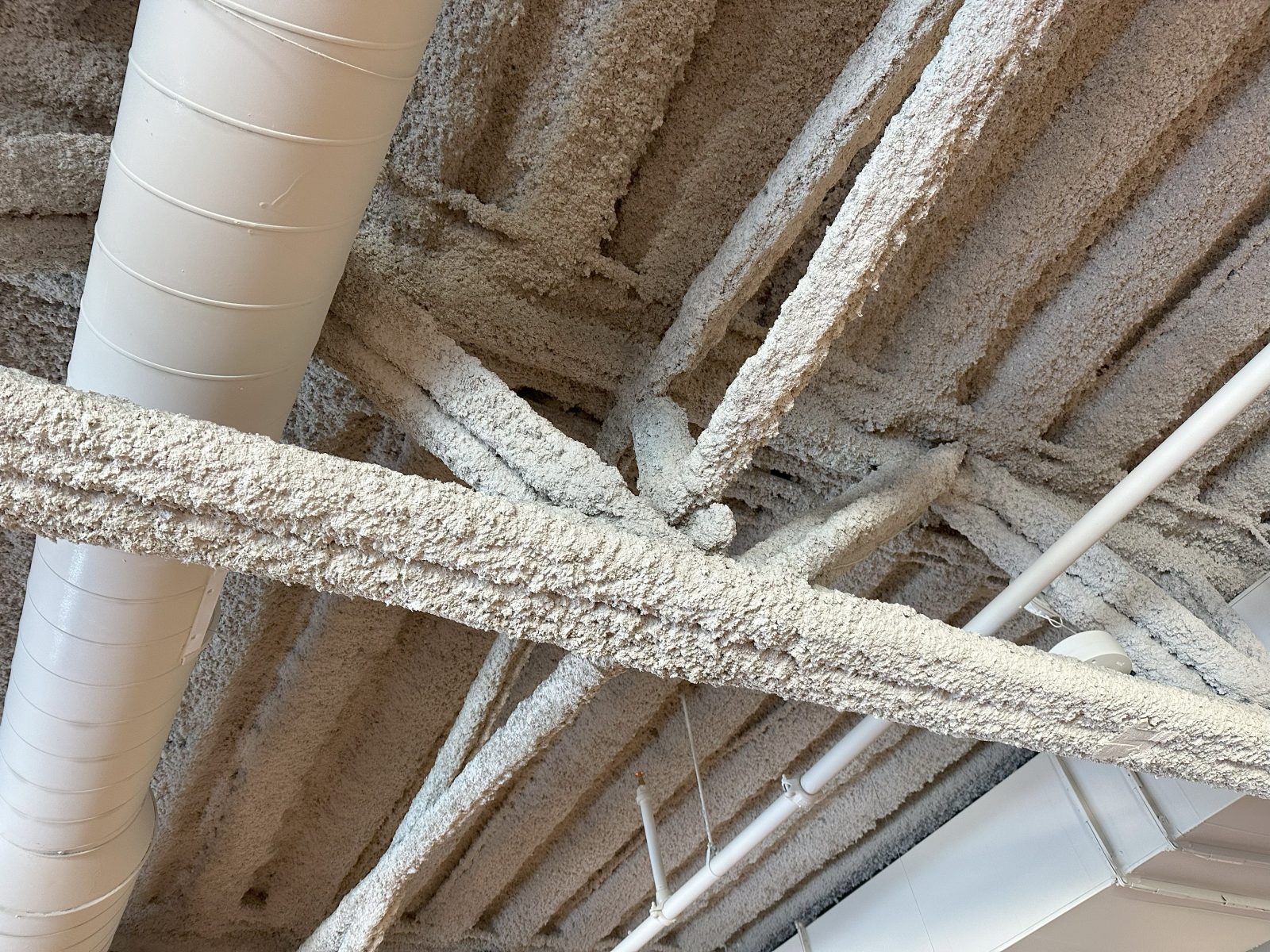
Fire retardant additives in other materials
Here is how other common materials are made fire-retardant:
- Wire coatings: Plastic wire coatings often contain aluminum trihydrate (ATH) and/or hydromagnesite.
- ATH works by releasing water vapor when subjected to heat. The endothermic reaction cools the surrounding area and acts as a vapor barrier.
- Hydromagnesite works in three ways. It first releases water vapor during decomposition. It then releases carbon dioxide at higher temperatures, which decreases the amount of oxygen present to fuel the fire. Finally, it stabilizes the formation of char, which minimizes smoke.
- Roofing membranes: Due to its chlorine content, polyvinyl chloride (PVC) in roofing membranes can resist ignition better than legacy materials. Other roofing materials, such as modified bitumen or ethylene propylene diene monomer (EPDM), rely on additives like ATH or other proprietary blends to achieve fire resistance. Proper installation and maintenance are essential to prevent issues like moisture infiltration or UV and thermal degradation, which can compromise their effectiveness.
- Insulation: New polystyrene insulations contain brominated styrene butadiene copolymer in foam board, a less-toxic alternative to the formerly used brominated and chlorinated organophosphate fire retardants. When bromides break down in the presence of heat, they release bromine radicals. These bromine radicals react with the high-energy hydrogen and hydroxide radicals present in the flames, which slows down the combustion process.
LABORATORY TECHNIQUES TO CHARACTERIZE UNKNOWN SFRMs
Multiple analytical tests can be employed to identify and characterize the components present in an unknown SFRM and compare those results to known samples and materials.
- Fourier transform infrared spectroscopy (FT-IR) reports on the chemical bonds present in a sample. By comparing the collected spectrum to a library of known materials, the main chemical components of materials such as gypsum (calcium sulfate; CaSO4) and portland cement (calcium silicates) can be identified. These chemical identifications can be used to characterize the type of SFRM material.
- Energy-dispersive X-ray spectroscopy (EDS) reports on the elements present on the surface of a sample when observed at high magnification using a scanning electron microscope (SEM). EDS can show elemental breakdown by atomic or weight percent, which allows researchers in the SGH Applied Science & Research Center (ASRC) to understand what molecules are present in the sample.
- Petrography is the classification of rocks (including the cement in some SFRMs) using microscopic analysis to describe the mineral composition, texture, and structure. This analysis is often performed on thin, transparent sections of rocks using a polarized microscope.
In a recent project, a sample of unknown SFRM material was submitted to SGH’s Applied Science & Research Center (ASRC) for chemical identification. Through combined FT-IR and EDS analysis, researchers identified a large sulfate peak in the FT-IR spectrum and high percentages of calcium, sulfur, and oxygen in the EDS spectrum. These results confirmed that the unknown SFRM is composed of calcium sulfate.
Additional petrographic analysis on a thin section of the unknown SFRM showed numerous, very fine, needle-like grains that were tentatively identified as bassanite (a calcium sulfate material). This identification aligns with the chemical analysis performed via FT-IR and EDS and adds additional context to the identity of the calcium sulfate material within the tested SFRM.
WHAT HAPPENS WHEN SFRM AND IFRM COATINGS FAIL?
Fire-retardant coatings can fail in several ways, and it is not always obvious why. In these cases, it is important to document conditions and test material samples to explore what may be happening. For example, SGH’s ASRC has seen several projects where SFRM was peeling and blistering, prompting our teams of engineers and scientists to investigate.
In a recent project, our engineers performed adhesion tests in the field and sent SFRM samples to the ASRC for failure analysis. Scanning electron microscope (SEM) imaging of the SFRM showed the presence of multiple layers of material, each varying in thickness, and containing different quantities of additives that we would expect to see based on the SFRM material’s safety data sheet.
Using a stereomicroscope, we also found cavities and defects in between layers, which were nonuniform in size and distribution. We also observed that when the material was exposed to water, it became soft and malleable, leading to potential warping and cohesion failures that were observed in the field.
Using these laboratory analyses, we suggested several root causes for the material failure:
- Improper mixing and material preparation before application, which led to adhesion and cohesion issues.
- Water infiltration beneath the SFRM and/or high humidity conditions, which compromised the integrity of the SFRM.
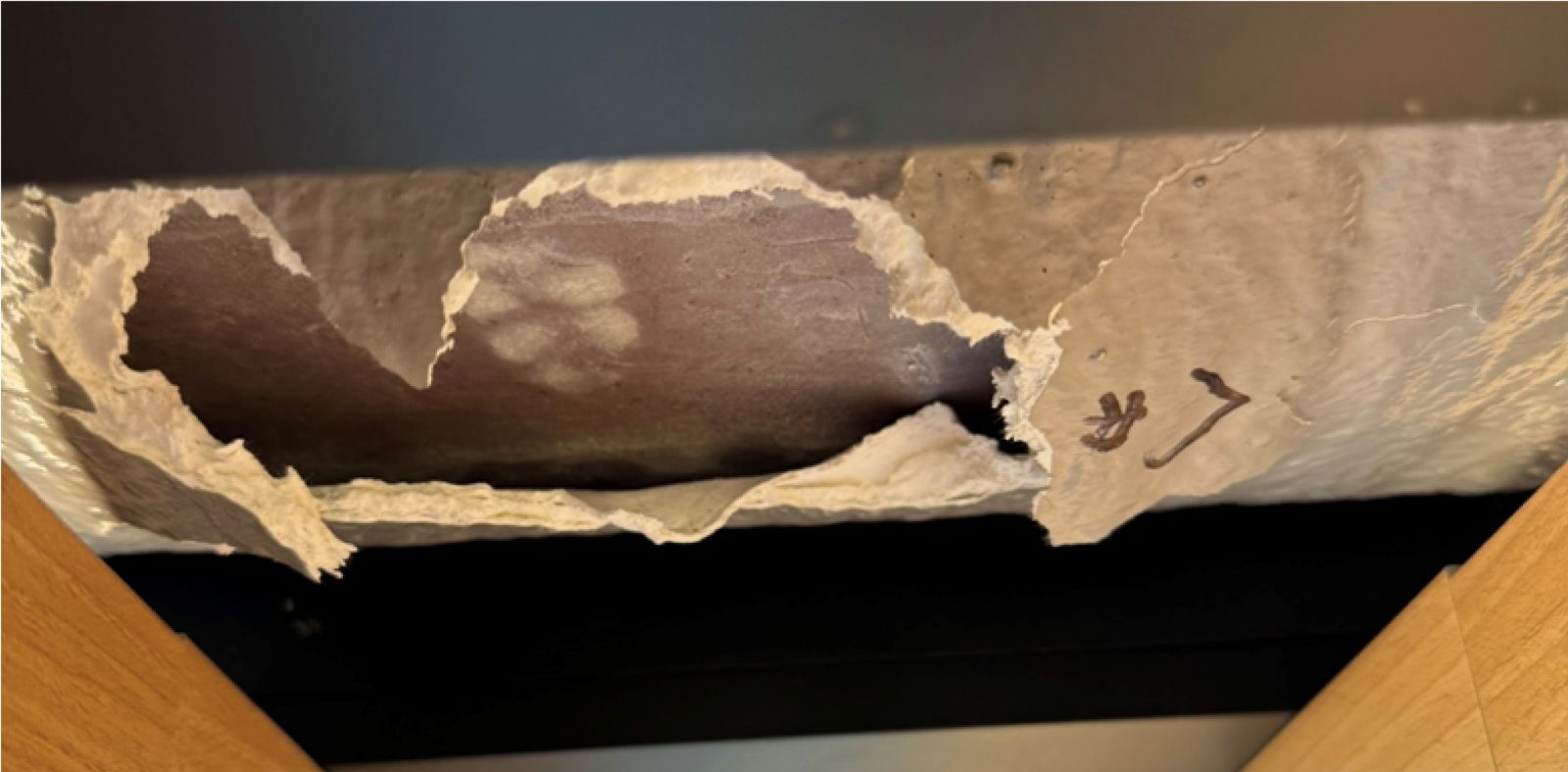
WHY THIS MATTERS
It is important to address these kinds of fireproofing failures immediately to restore fire protection to steel structures. Fireproofing is only effective if done right, and as we’ve seen in many cases, coatings are only as good as their surface preparation. Failures like the one we investigated can leave structures vulnerable, and addressing these issues is critical to restoring fire protection and maintaining compliance with building and fire codes.