Navigating the Challenges of MCM Rainscreen Cladding
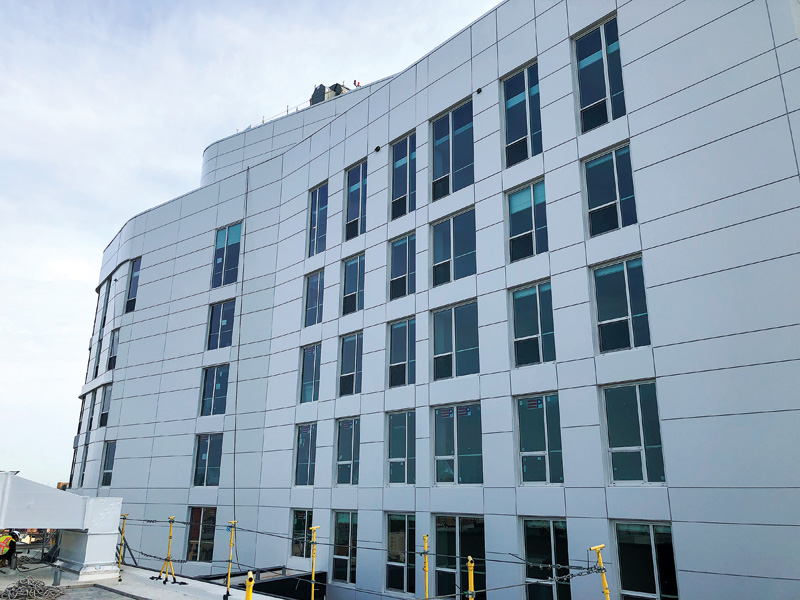
Metal Composite Material (MCM) rainscreen cladding systems have been popular for decades due to their versatility in various cladding applications. They often perform well for many years when designed, fabricated, and installed appropriately. However, improperly executed systems can cause issues for building owners and project teams. This article will explore key aspects of MCM cladding, lessons learned from past projects, and best practices for future applications.
Sheet MCM panel material generally consists of two thin sheet-metal “skins” with an inner non-metal core. The metal skins, typically aluminum (though sometimes other metals), are approximately 0.5 mm (0.020 in.) thick and cover both sides of a plastic-based or a mineral-plastic core, which is approximately 3 to 5 mm (0.12 to 0.2 in.) thick. Unlike sheet metal, MCM panels cannot be easily bent, so grooves are routed into the backside of the material to allow for bending, leaving only the outer sheet metal skin at back-routed conditions. Stiffeners, usually aluminum extrusions, are often used to reinforce panels and panel edges to help increase rigidity, limit distortion and deflection, and facilitate attachment.
Publisher
Metal Architecture