Assessing Thermal Performance with sUAS and Drone Technology
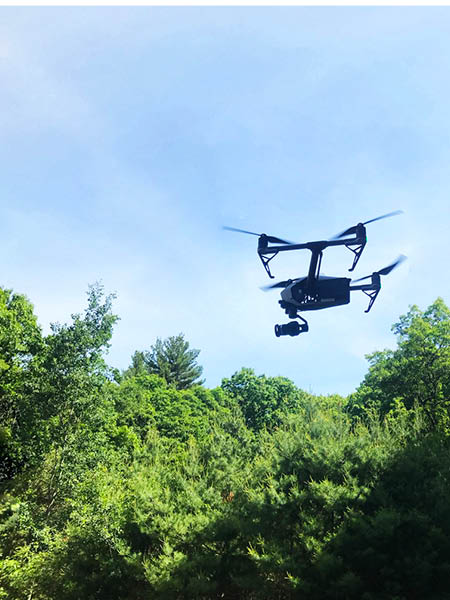
When used appropriately, small unmanned aircraft systems (sUAS) and other drone technologies can make critical—and sometimes dangerous—facade assessments more efficient, precise, and accessible for team members across the architecture, engineering, and construction (AEC) industry. Traditional direct inspection methods from the ground or using aerial lifts have shortcomings that an sUAS or drone can overcome.
Increasingly, AEC practitioners are using sUAS and drones to perform thermal imaging scans of building enclosures to detect air, moisture, and heat leakage from a building enclosure. Infrared scans that could potentially take days to perform can now take significantly less time while providing better and more comprehensive infrared images. However, these methods require careful planning and an understanding of relevant industry standards and technology best practices to achieve reliable and actionable results. By using sUAS and drone technology correctly, AEC professionals can get detailed results to make informed recommendations that address underlying building concerns.
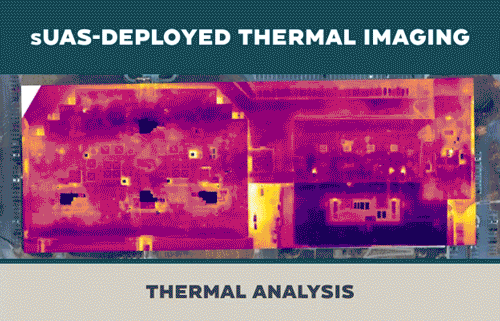
Thermal Imaging Approaches and Standards for Building Enclosures
Water infiltration, moisture accumulation, air leakage, and thermal bridging are among the most common and costly building enclosure failures, causing damaged interior finishes, increased energy consumption, and mold growth within walls. Infrared thermography, or thermal imaging, is often used to detect and determine the extent of these failures and can also be used to detect thermal bridging, missing wall insulation, insulated glass unit failures, and concrete delamination.
The industry has issued standards and other guidance for these test methods. The two most common standards for new and existing buildings are:
- ASTM C1153, Standard Practice for Location of Wet Insulation in Roofing Systems Using Infrared Imaging: Outlines necessary conditions and techniques to determine the location of wet insulation in roofing systems. Addresses criteria for equipment, weather parameters, operating procedures, and invasive openings.
- ASTM E1186, Standard Practices for Air Leakage Site Detection in Building Envelopes and Air Barrier Systems: Covers the procedure for qualitatively locating air leakage in building enclosure and air barrier systems.
The industry has used handheld infrared cameras to assess building enclosures for many years. However, developments in sUAS technology have made thermal imaging safer, more cost-effective, and more accessible. These approaches have also improved data clarity and expanded the possible range of thermal imaging applications to water leakage into concealed wall spaces or the interior. If the building loses window or curtain wall glass, it can experience increased internal building air pressure due to wind and contribute to structural, roofing, or interior wall damage.
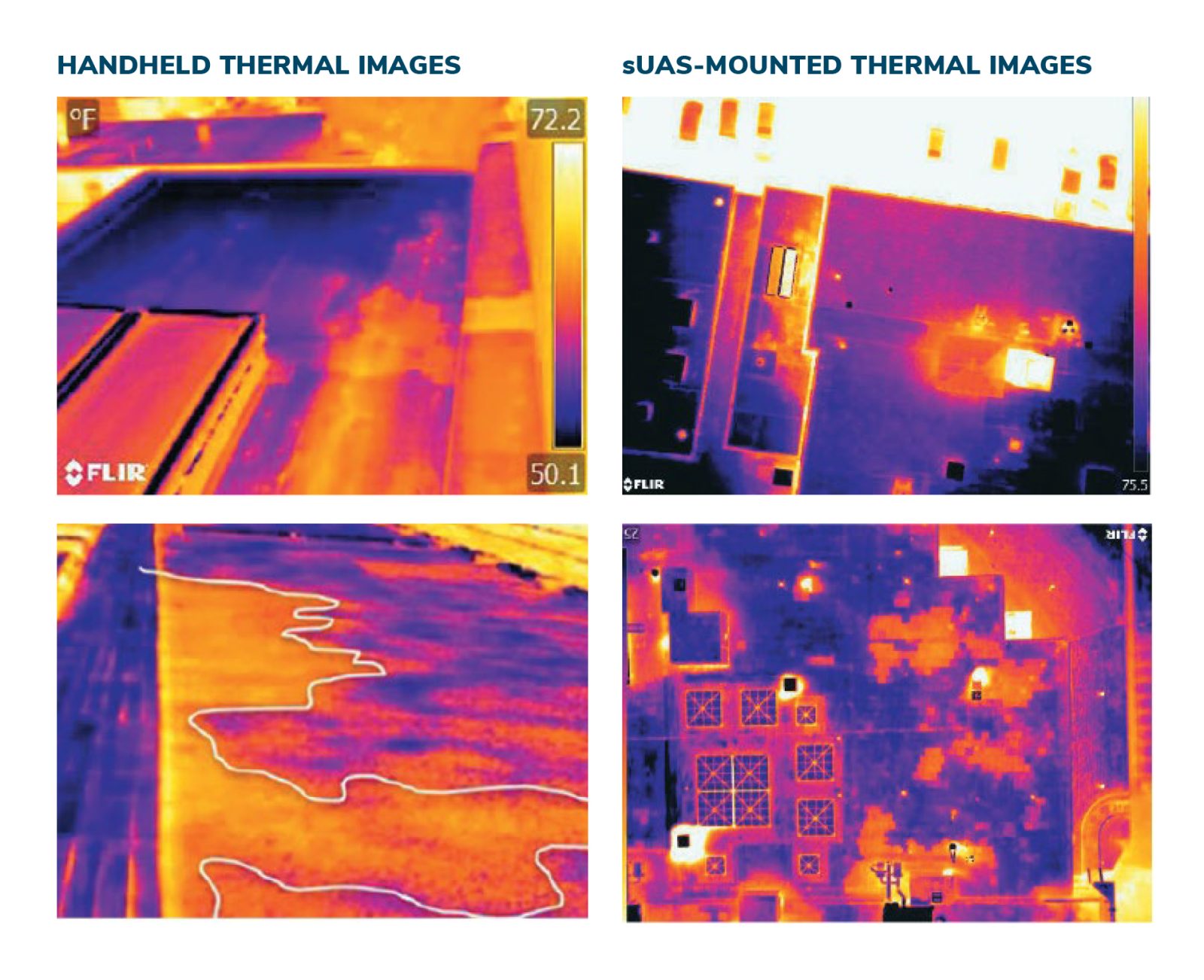
Using sUAS and Drone Methods for Thermal Imaging
Benefits
As thermal imaging has gained traction, sUAS technology has improved and become more accessible. Using sUAS to perform infrared scans of building enclosures has improved the process and results in several ways.
Time and Cost Efficiencies: Infrared scans of roofing assemblies using handheld cameras are commonly performed from the roof level on a ladder at night, which has inherent safety concerns. This can take several hours to perform, whereas an sUAS-mounted camera can capture the same roof area in minutes.
Environmental Parameters: Mounting an infrared camera to an sUAS provides a wide field of vision and apparent surface temperatures are shown relative to adjacent materials over a larger area, which minimizes the effect of minor apparent surface temperature differences and reveals more widespread thermal anomalies associated with wet roofing materials or air leakage. This allows for infrared scans to be performed during a wider range of conditions.
Reflections: Infrared images are most accurate when taken looking directly perpendicular to the surface being scanned to avoid reflections from adjacent surfaces that can mask thermal anomalies associated with water or air leakage. Comparatively, an sUAS-mounted camera offers greater flexibility to take photographs from various distances and angles.
Aggregate Ballast Roof Systems: The thermal patterns associated with aggregate ballast over roofing membranes are often indistinguishable from “hot spots” associated with areas of wet insulation. sUAS images can display a larger area, which can mute localized anomalies and reveal more widespread issues.
Quality of Data, Ease of Analysis: The quality of data and deliverables provided by an sUAS infrared scan is generally superior to what handheld infrared camera scans produce. Capturing larger areas of the roof in individual or stitched images allows design professionals to see a holistic infrared view of the roof that can be easily analyzed to identify larger patterns, which are more difficult to discern when reviewing many individual images.
Challenges
sUAS and drone technology can minimize many of the obstacles encountered when performing infrared scans using a handheld camera. However, challenges and limitations still exist.
Operator Requirements: All commercial sUAS operations are regulated by the Federal Aviation Administration (FAA) and require a certified operator to perform the work.
Location Challenges: The FAA outlines airspace restrictions for project sites, including maximum allowable altitude above ground level. If a project is near an airport, some additional authorization may be required.
Education and Certification: Some pilots are experienced sUAS operators but lack an understanding of infrared technology and ASTM standards. Their scans may be performed under incorrect environmental conditions or with ineffective methodologies.
Data Collection: sUAS data analysis is usually performed in office after the images are downloaded, which does not allow thermographers to take additional infrared images or assess thermal anomalies in person at the time of the scan.
Data Processing: There is limited software available that can effectively stitch infrared images into one complete building image because of the amount of data involved—each pixel on an infrared image is embedded with measurable temperature data.
Conclusion
Building owners and property managers can use infrared thermography as a quality control process on new buildings, to detect air or water leakage in existing enclosures, and to evaluate the efficacy of repairs, among other applications. sUAS and drones can significantly reduce the time and cost of data capture, eliminate issues related to access and safety that are present when using a handheld camera at night, allow for scans to be performed during a wider range of environmental conditions, and improve the overall quality of images that are captured, resulting in a better end product.
Though there are many advantages, the decision to employ an sUAS to perform an infrared scan must be carefully considered. It is critical to confirm that the sUAS operator is certified, trained, and educated on the applicable ASTM standards and understands the nuances associated with infrared thermography. It is also essential that the data be collected in a way that it will provide the most useful deliverable for the project’s specific goals.
This topic brief is adapted from “Small unmanned Aerial System Applications in the Building Enclosure Industry: Using Thermal Imaging to Assess Building Performance,” which was presented at the 2021 IIBEC International Convention and Trade Show and published in the December 2022 issue of the IIBEC Interface.