Savage, MN
Salt Processing Dome
Scope/Solutions
The salt processing dome, with an inside diameter of 173 ft and a dome peak of 65 ft, houses equipment for processing and packaging bulk rock salt for commercial sale. The shell structure was constructed in 1985 by placing a nominal 3-1/2 in. of shotcrete over an inflatable fabric dome formwork. The concrete dome was exhibiting signs of deterioration and needed repairs to extend its useful life. SGH evaluated the dome’s condition and designed repairs.
Uninterrupted access to the salt processing dome is critical to the facility’s function. SGH performed a snap-through buckling analysis, evaluated the dome’s structural capacity, and designed repairs that would minimize disruption to plant operations. Highlights of our design include the following:
- Rebuilding nine door openings by adding new eyebrow slabs and side walls to stiffen the openings in the dome shell
- Infilling existing skylights with reinforced concrete
- Performing localized concrete repairs, including installing galvanic anodes in the repair areas
- Pressure injecting cracks with epoxy
- Strengthening the upper stiffening ring with two layers of bi-directional glass fiber-reinforced polymer
- Replacing and retensioning existing internal post-tensioning tendons extending between door openings in the wall, and adding hoops at the anchorages to address localized high-stress zones in the thin shell
- Adding six external post-tensioning tendons above the door openings, anchoring the tendons to the dome with new stainless steel eye bolt deviators, and stressing the tendons from two vertical lines of dogbone anchors
- Recoating the dome with a spray-on insulation and membrane to protect the external tendons
Project Summary
Key team members
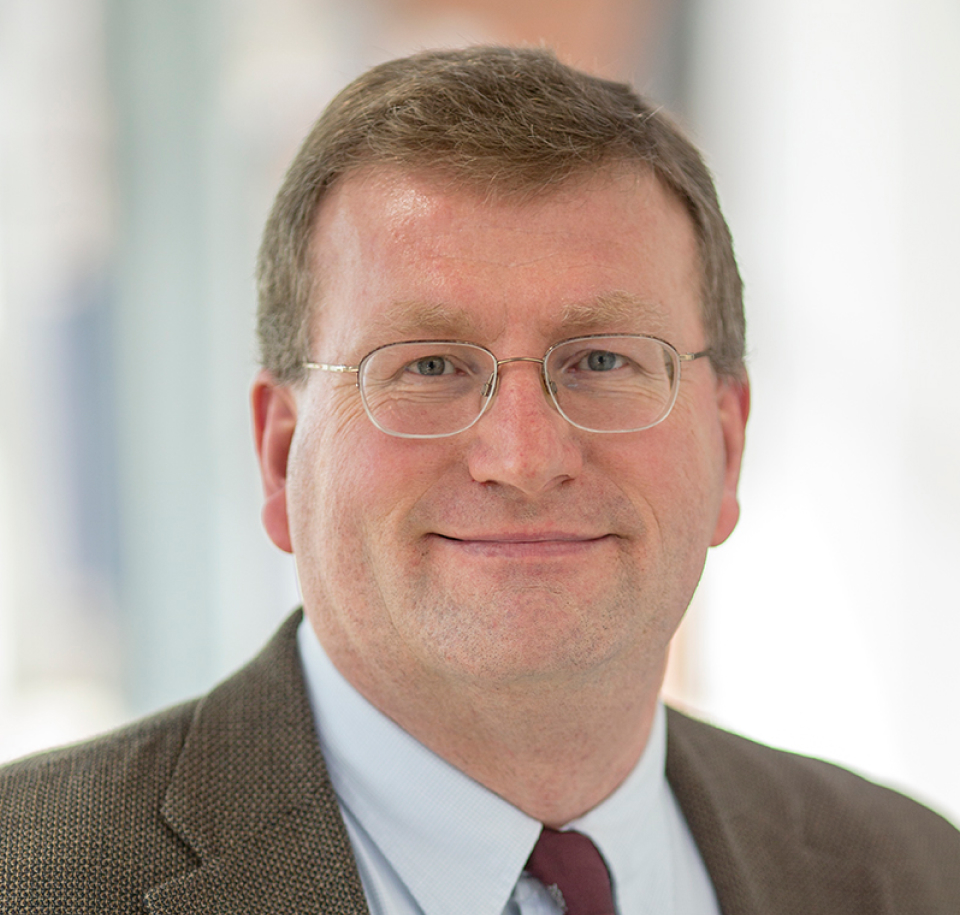
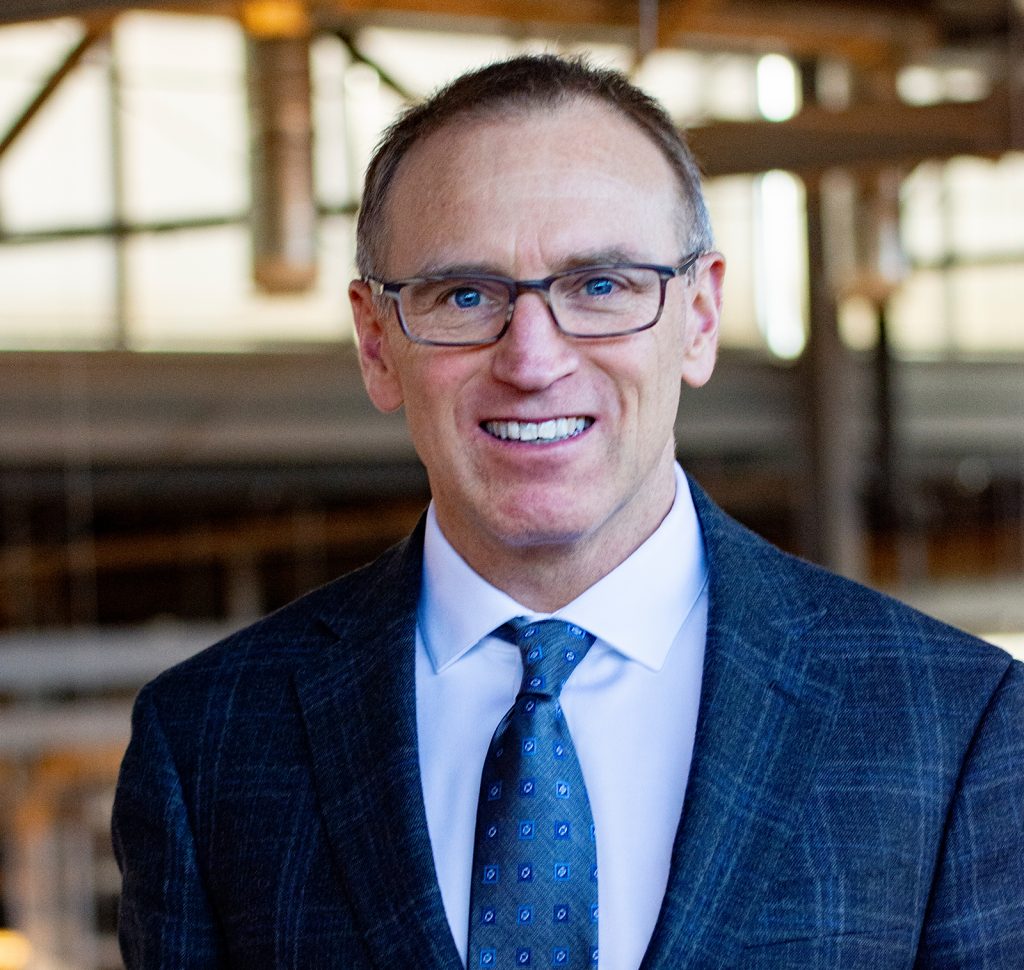